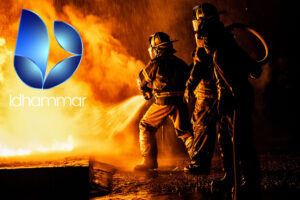
Enhancing Emergency Response: The Role of Maintenance Management Software for the Emergency Services
Read More »
September 6, 2023
No Comments
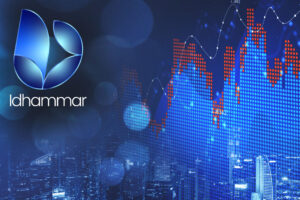
What Would 10% Less Downtime Do to Your Bottom Line? How Maintenance Management Software Boosts Profits
Read More »
August 15, 2023
No Comments